Why Tariffs Won’t Bring Back Blue-Collar Jobs
The promise that tariffs will restore lost American manufacturing jobs appeals to economic nostalgia. But the reality is far more complex. While some national security sectors may benefit from reshoring, broad tariffs are not an effective job-creation tool. In fact, they often impose costs that outweigh potential gains. Here’s a detailed look at why tariffs aren’t the answer.
China’s Manufacturing Lead Isn’t About Cheap Labor Anymore
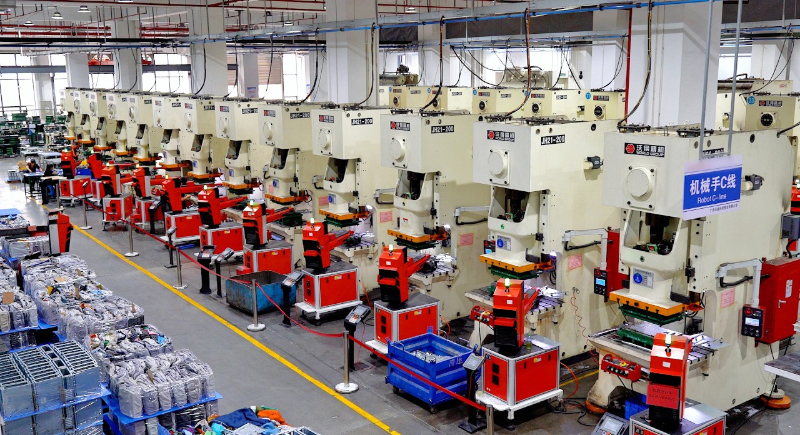
Credit: Youtube
China is no longer a low-cost labor economy. It has become the world’s most advanced manufacturing hub that’s investing heavily in robotics, automation, education, and scale. American factories would struggle to match this capacity, even with significant investment. Tariffs don’t reverse decades of structural development; they simply isolate U.S. firms from a more efficient supply chain.
Most U.S. Manufacturing Today Requires Fewer Workers
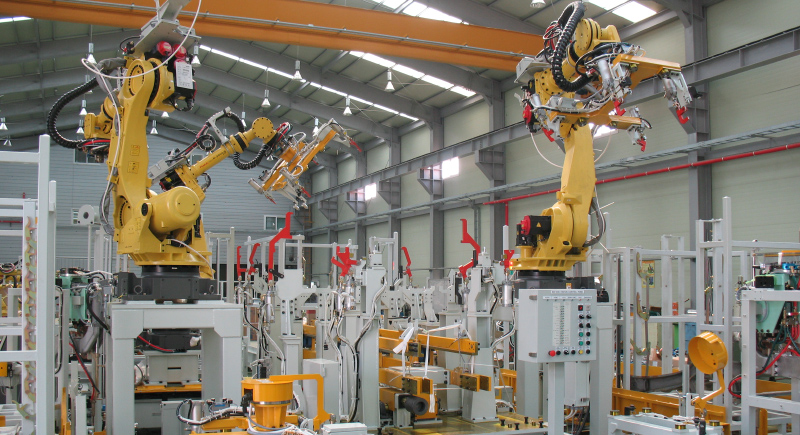
Credit: Wikimedia Commons
Modern manufacturing is increasingly automated. Even if domestic production increases, it won’t create mass employment. Jobs in advanced manufacturing often require technical skills and degrees, not manual labor. Tariffs may shift some production home, but the jobs created will be limited and specialized—not the widespread blue-collar employment of decades past.
Tariffs Raise Consumer and Business Costs Without Adding Value
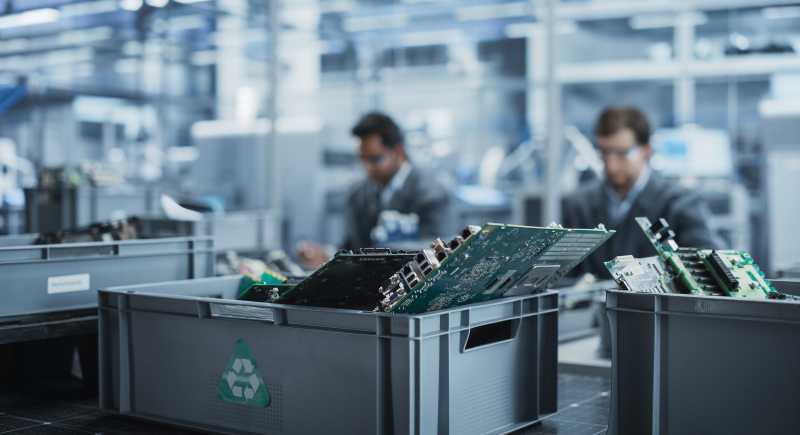
Credit: iStockphoto
When tariffs increase input costs, those expenses are passed down the supply chain. This affects consumers directly through higher retail prices and businesses through tighter margins. The result is inflationary pressure across multiple sectors, especially in goods like electronics, appliances, and vehicles. Job creation, if any, is marginal and comes at a significant economic cost.
Domestic Manufacturing Is Still Far More Expensive
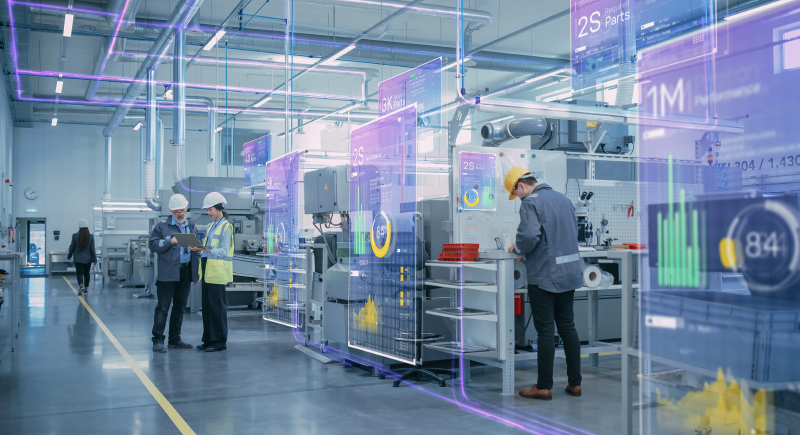
Credit: iStockphoto
Building products in the U.S. involves higher costs across the board—raw materials, packaging, tooling, and domestic logistics. Many American manufacturers report difficulty sourcing materials and skilled labor locally. These factors make it nearly impossible to match overseas production costs, even with tariff protections, especially in lower-margin consumer markets.
The U.S. Has a Skilled Labor Shortage in Key Sectors
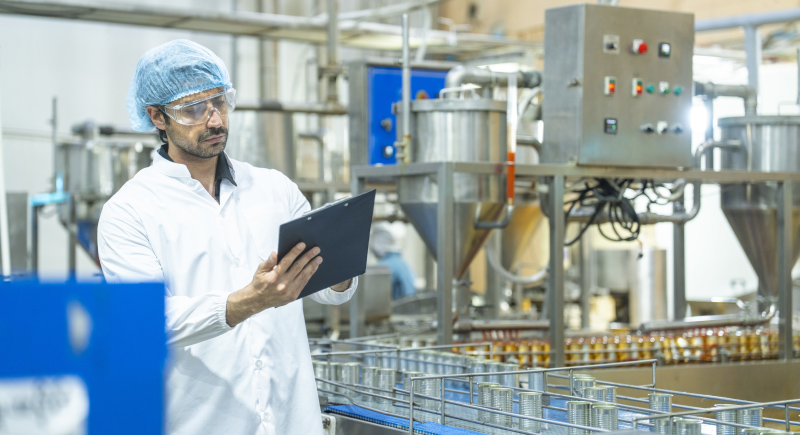
Credit: iStockphoto
Manufacturing jobs in the U.S. increasingly require medium to high technical skills, including repair, machine operation, and systems maintenance. These roles are difficult to fill domestically due to decades of declining investment in vocational training and trade education. Without a pipeline of skilled labor, reshoring production will not significantly impact blue-collar employment.
U.S. Supply Chains Lack the Infrastructure to Compete
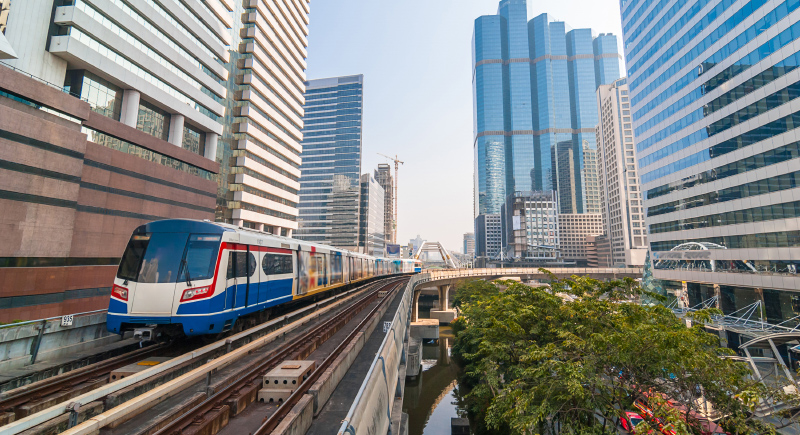
Credit: iStockphoto
Internal shipping and logistics costs in the U.S. are significantly higher than in Asia. Factors include aging rail systems, high fuel prices, a shortage of truck drivers, and limited internal waterways. Even when manufacturing returns to the U.S., the cost of distribution often offsets any perceived competitive advantage from reshoring.
Small Businesses Are Hit Hardest by Tariffs
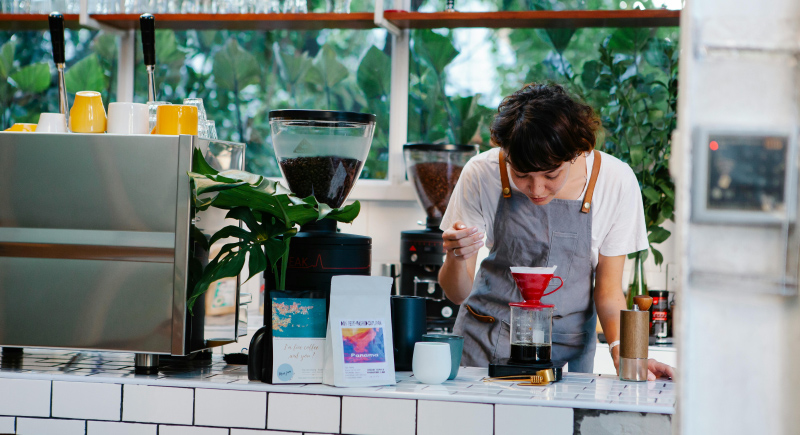
Credit: pexels
Many American-owned businesses rely on imported materials and components to remain viable. Tariffs increase their operating costs without providing the volume or efficiency of scale enjoyed by multinationals. As a result, some businesses are forced to downsize, relocate, or shut down entirely—undermining local employment and reducing domestic output.
Nearshoring Often Just Reroutes Chinese Input
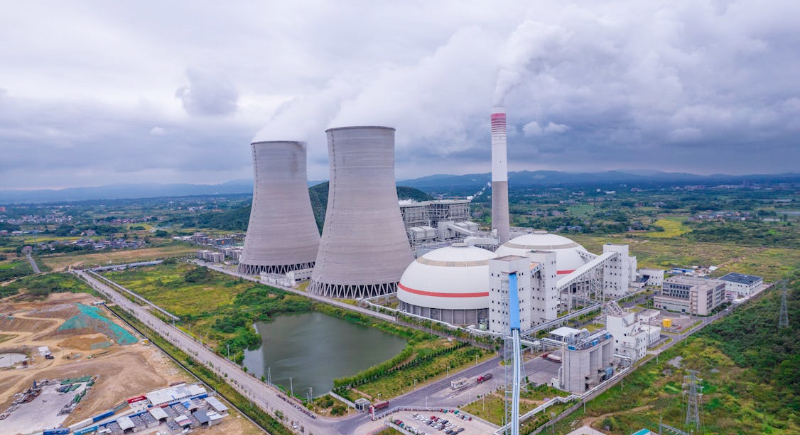
Credit: pexels
While some manufacturing has shifted to Mexico and Southeast Asia, many of these operations still depend on Chinese raw materials or component parts. Chinese firms have established a strong presence in neighboring countries, which has enabled U.S. firms to access cheaper inputs under the guise of reshoring. Tariffs on China alone do not eliminate dependence on its manufacturing base.
U.S. Manufacturers Still Rely on Chinese Inputs
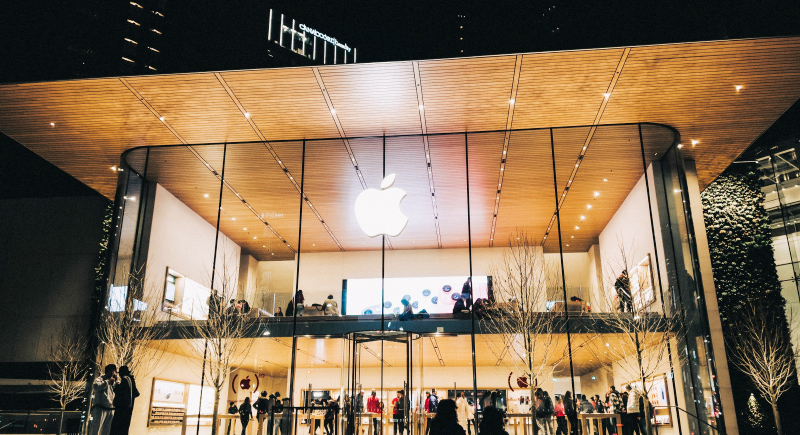
Credit: pexels
Many U.S. manufacturers, including major players like Apple and Boeing, continue to rely on components produced in China. Replacing these supply chains is not just expensive—it’s logistically difficult. For some industries, there is no domestic alternative. Attempting to localize production through tariffs alone risks increasing costs without achieving supply chain independence.
Raw Material Access Is a Critical Weakness

Credit: iStockphoto
China controls or refines many critical raw materials used in semiconductors, electric vehicles, and advanced electronics. According to the U.S. Geological Survey, China is the primary supplier of over half of the mineral commodities deemed essential to national security and economic function. Without access to these materials, large-scale domestic manufacturing remains constrained.
The Shenzhen Model Can’t Be Replicated Quickly
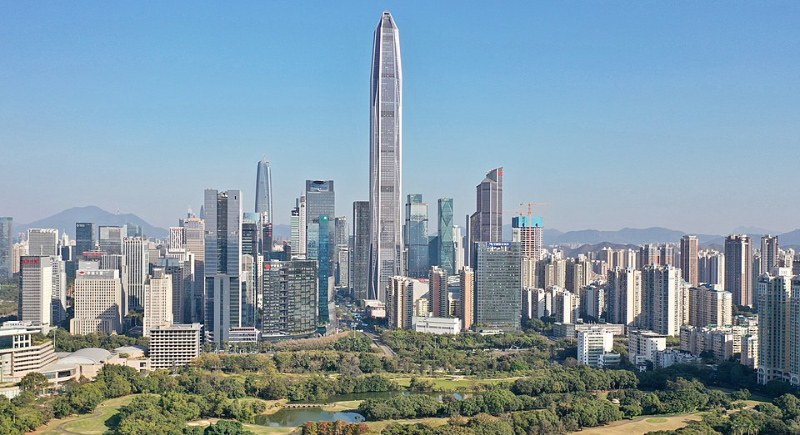
Credit: Wikimedia Commons
China’s dominance in electronics manufacturing stems from decades of coordinated policy, foreign investment, and infrastructure development, particularly through Special Economic Zones like Shenzhen. Replicating this model in the U.S. would require long-term investment, coordinated planning, and major educational reform. Tariffs do not provide the capital or structure to build a comparable ecosystem.
Tariffs Often Undermine Existing U.S. Manufacturing
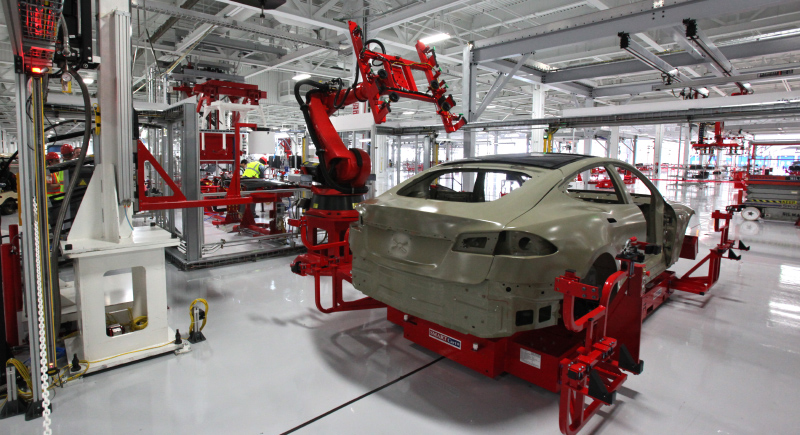
Credit: Wikimedia Commons
Increased input costs caused by tariffs can reduce the competitiveness of U.S.-based manufacturers—especially those already operating on tight margins. Some companies have relocated operations abroad in response to tariffs, citing the inability to source components domestically or absorb cost increases. In these cases, tariffs can actually accelerate offshoring.
National Security Requires Targeted Policy, Not Blanket Tariffs
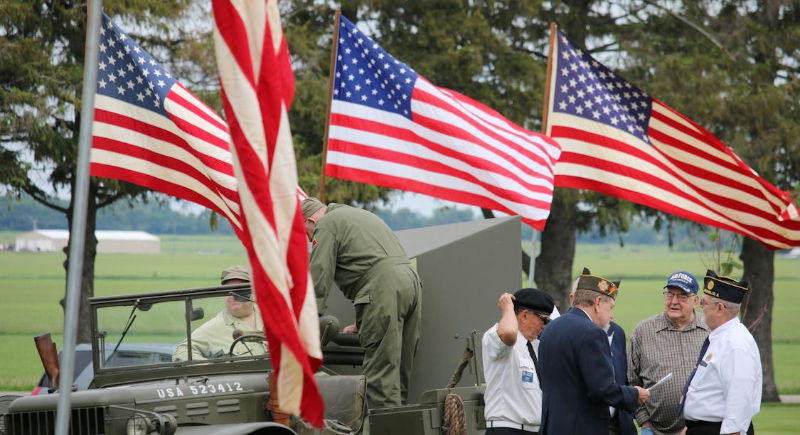
Credit: pexels
There is a legitimate need to restore the production of certain strategic goods, such as semiconductors, batteries, and military hardware. However, addressing this requires targeted subsidies, public-private partnerships, and long-term investment, not broad tariffs. Using tariffs as a catch-all strategy risks distorting markets and misallocating resources that should be focused on national security priorities.
The CHIPS Act and Industrial Legislation Show the Right Approach
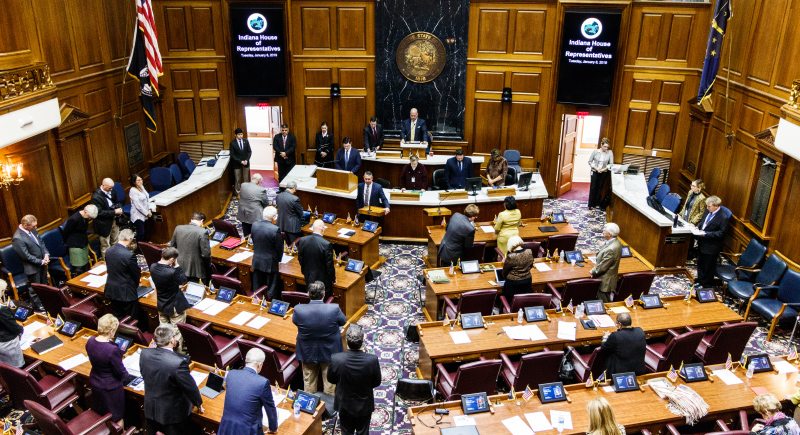
Credit: iStockphoto
Recent U.S. legislation, including the CHIPS Act, the Infrastructure Investment and Jobs Act, and the Inflation Reduction Act, channels funding into critical sectors. These measures focus on capacity building, not protectionism. Reshoring must be approached strategically—by fostering innovation, supporting infrastructure, and developing workforce skills—not simply by taxing imports.
Tariffs Offer Political Simplicity, Not Economic Solutions
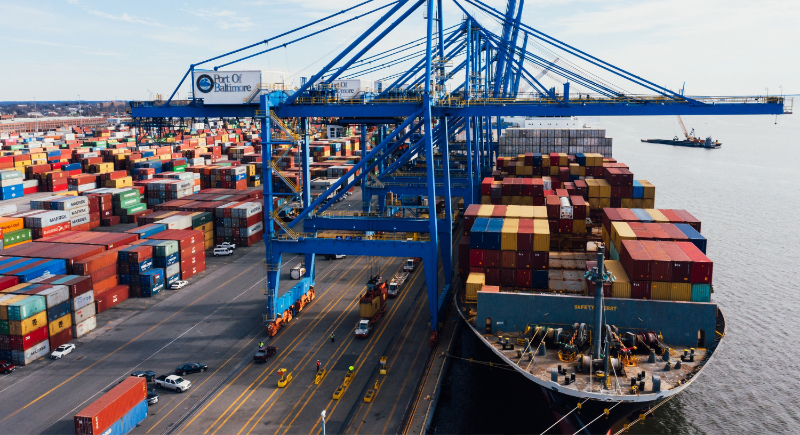
Credit: pexels
The appeal of tariffs lies in their simplicity: a clear policy lever with immediate impact. However, they offer no comprehensive solution to the challenges facing U.S. manufacturing. Structural change requires patient investment, regulatory reform, workforce development, and supply chain redesign. Tariffs alone cannot address the root causes of industrial decline.